Level Measurement Selection Guide: 5 Key Questions to Choose the Right Instrument
In industrial environments, the proper selection of level or point level instruments has a direct impact on process stability, equipment safety, and maintenance costs. With a wide range of devices available on the market, how can you make the right choice? This guide offers a clear “application Q&A” approach to help engineers and plant operators quickly identify the most suitable level measurement solution.
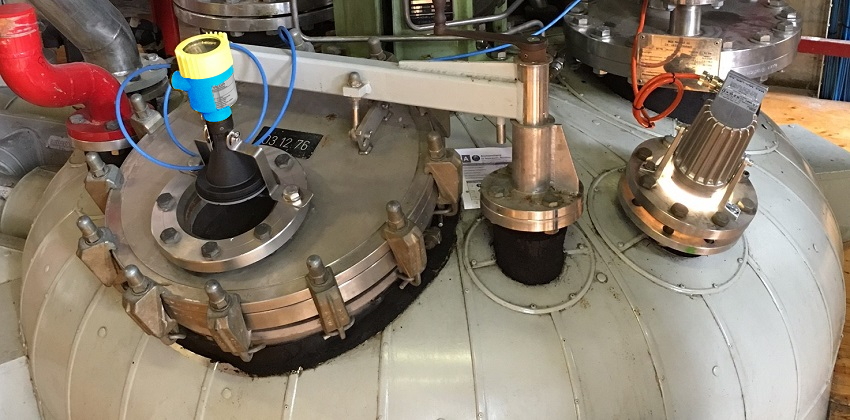
Q1: What is the level measurement medium—liquid or solid?
This is the first and most fundamental question when selecting a measurement instrument:
- For liquids such as water, oil, acid, slurry, or solvents — choose a liquid level transmitter
- For solids such as powder, grains, cement, or ash — use a point level switch or bulk solids level transmitter
Note: For high-viscosity liquids, foaming surfaces, or processes involving steam, make sure to select an instrument compatible with complex fluid dynamics.
Q2: Does the probe need to contact the medium?
Depending on hygiene requirements and media characteristics, measurement methods are categorized as:
- Contact-based: magnetic flap, float, tuning fork, capacitive, guided wave radar — ideal for standard liquids in open tanks
- Non-contact: radar level transmitters and ultrasonic sensors — preferred for high-temperature, corrosive, or adhesive media
For food, pharmaceutical, or highly corrosive applications, non-contact radar level transmitters are strongly recommended. Compared to ultrasonic sensors, radar offers higher signal penetration and better accuracy under interference-prone conditions.
Q3: What are the temperature and pressure conditions?
Process temperature and pressure are critical parameters that influence selection:
Process Condition | Recommended Instrument |
---|---|
High temperature (>120°C) | Ultrasonic is unsuitable; use high-temperature radar or guided wave radar |
High pressure (>1MPa) | Use sealed models with flange mounting |
Steam or volatile gas | Use 80GHz radar with narrow beam angle and strong anti-interference capabilities |
For low-temperature environments (e.g., -40°C and below), make sure to select instruments rated for cryogenic applications to avoid measurement failure due to freezing.
Q4: Is the container or tank shape complex?
Tank or silo geometry has a significant impact on wave reflection and measurement stability. Consider the following:
- Large storage tanks or spheres: use long-range radar level transmitters with wide measuring range and high accuracy
- Small tanks, dosing vessels, or IBCs: select compact radar models with narrow beam angles and small antennas
- Conical silos or hoppers: avoid placing the sensor directly above the inlet; take dust and buildup into account
If the container includes stirrers, internal pipes, or heating coils, choose radar transmitters with adjustable mounting brackets to fine-tune angle and avoid false echoes.
Radar transmitters with narrow beam angles offer strong signal focus and better penetration.

Q5: What output signal is required? Will it integrate with control systems?
Choose an output type that matches your automation system needs:
Output Type | Application Scenario |
---|---|
4–20mA (2-wire loop) | Standard analog output widely used with DCS/PLC |
HART / RS485 / Modbus | Digital communication for remote diagnostics and system integration |
Switch output | Useful for high/low level alarms or pump control |
Bluetooth or Wireless | Ideal for decentralized tank farms or remote monitoring |
If your plant uses DCS, PLC, or SCADA systems, confirm protocol compatibility and power requirements before selecting the device.
Summary: 5-Step Selection Checklist
“Identify medium → choose contact type → assess process conditions → evaluate tank shape → define signal needs.”
If you’re still unsure which level instrument fits your application, prepare the following details and consult your instrument supplier:
- Medium type and physical characteristics (foaming, steam, buildup)
- Temperature and pressure range
- Tank size, structural diagram, and available installation space
- Accuracy requirements, local display, or remote monitoring needs
- Signal output format and control system compatibility
For specialized applications, feel free to contact Shenzhen Jiwei Automations Ltd. We offer cost-effective, reliable, and field-proven level measurement solutions tailored to your plant conditions.
Whether you’re choosing a radar level transmitter for bitumen, slurry, acids, or granular materials, Jiwei’s technical team can help you select the best-fit product with long-term stability and minimal maintenance.