Magnetic Level Gauge vs. Glass Tube Level Gauge: Unleashing Superior Precision and Durability
Liquid level measurement is a critical aspect of industrial process control, and selecting the appropriate level gauge directly impacts system safety and operational efficiency. Glass tube and magnetic level gauges are two commonly used devices; however, under the guidance of industry standards such as GB/T 21446-2008: Magnetic Level Gauge, magnetic level gauges are increasingly recommended due to their superior durability, safety, and automation capabilities. This article provides a detailed comparison of the two instruments, highlighting the advantages of magnetic level gauges.
Comparison of Measurement Principles
Glass Tube Level Gauge
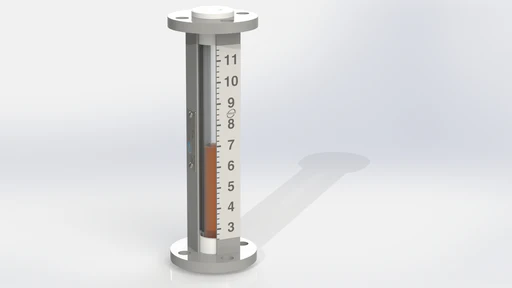
The glass tube level gauge operates based on the principle of communicating vessels. Changes in the liquid level within the container are directly reflected in the transparent glass tube, allowing the operator to visually observe the level. Some models feature a graduated scale to improve readability.
Magnetic Level Gauge
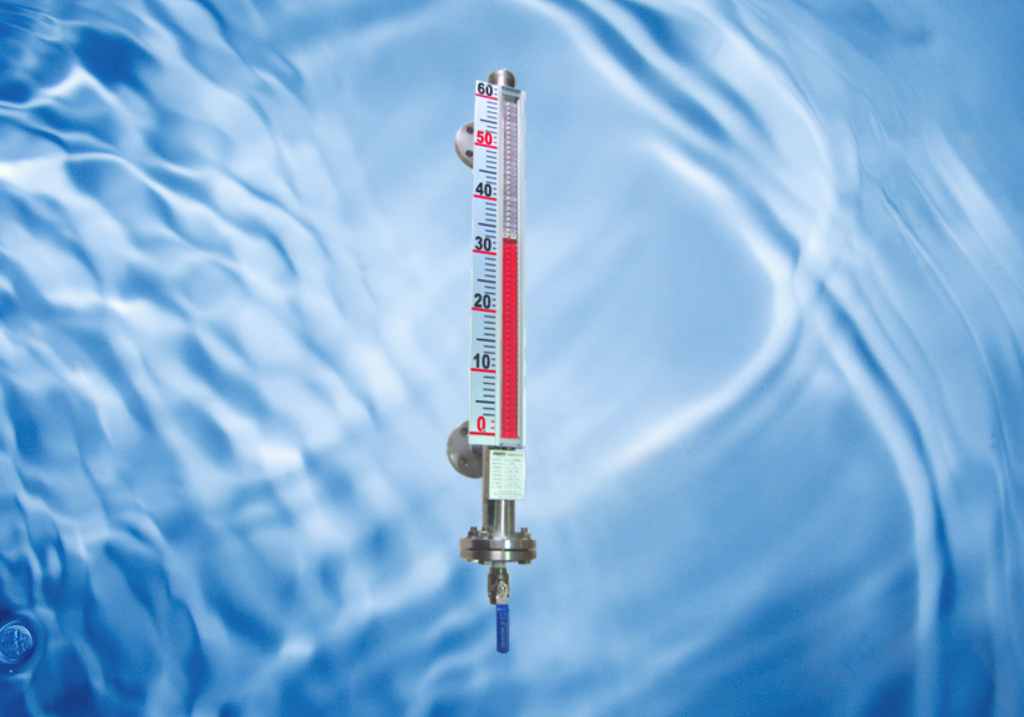
The magnetic level gauge utilizes buoyancy and magnetic coupling principles. A magnetic float inside the measuring chamber moves up and down with the liquid level, driving an external indicator equipped with bi-color flippers to display the liquid level. Modern magnetic level gauges can be integrated with remote transmitters (e.g., 4-20mA, current loop, HART protocol) for automated monitoring and alarm functions.
Comparison of Application Conditions
Industry standard GB/T 21446-2008 outlines the application conditions for magnetic level gauges, which can withstand high temperatures (>400°C), high pressures (up to 10MPa), and highly corrosive media. In contrast, glass tube level gauges have a more limited range, typically suitable for moderate temperatures (<150°C, with special models reaching higher), low pressures (<1MPa), and non-corrosive media.
Comparison Factor | Glass Tube Level Gauge | Magnetic Level Gauge |
---|---|---|
Temperature Range | Standard models: <150°C; Special glass models reaching higher | Can withstand temperatures >400°C |
Pressure Range | Low pressure (<1MPa) | Standard models up to 6.3MPa; High-pressure models up to 10MPa |
Corrosion Resistance | Limited; requires special materials for corrosive environments | Available in stainless steel, PTFE-lined, and other corrosion-resistant materials |
Vibration Resistance | Fragile, not resistant to vibrations | Robust construction, strong vibration resistance |
Leakage Prevention | Prone to breakage; models with protective casings or dual-layer glass reduce risks | Fully sealed design, no leakage risks |
Comparison of Safety
Safety is paramount in liquid level measurement, particularly in industries such as petrochemicals, chemical processing, and pharmaceuticals, where leaks can lead to serious accidents.
- Glass tube level gauges present significant safety risks if unprotected, as glass is fragile and can break under high temperatures or pressure fluctuations, potentially causing liquid spills or operator injuries. Some models incorporate protective covers, wire mesh reinforcements, or dual-layer glass to mitigate breakage risks.
- Magnetic level gauges feature a fully sealed design, eliminating the risk of glass breakage. This makes them particularly suitable for measuring toxic, flammable, and hazardous liquids such as chemical solvents and liquefied gases. Consequently, in liquid level safety management systems, magnetic level gauges are often the preferred choice.

Readability and Remote Monitoring Capabilities
- Glass tube level gauges have limited visibility, as the liquid level must be read at close range and under adequate lighting conditions, making remote monitoring impractical.
- Magnetic level gauges offer enhanced visibility and remote transmission capabilities. The bi-color flip indicator ensures clear level readings, even in standard lighting conditions. However, in extremely dark environments, additional illumination or reflective coatings may be necessary for improved readability. Additionally, magnetic level transmitters convert the level signal into 4-20mA or HART output, enabling seamless integration into DCS (Distributed Control Systems) or SCADA (Supervisory Control and Data Acquisition Systems) for automated monitoring and remote control.
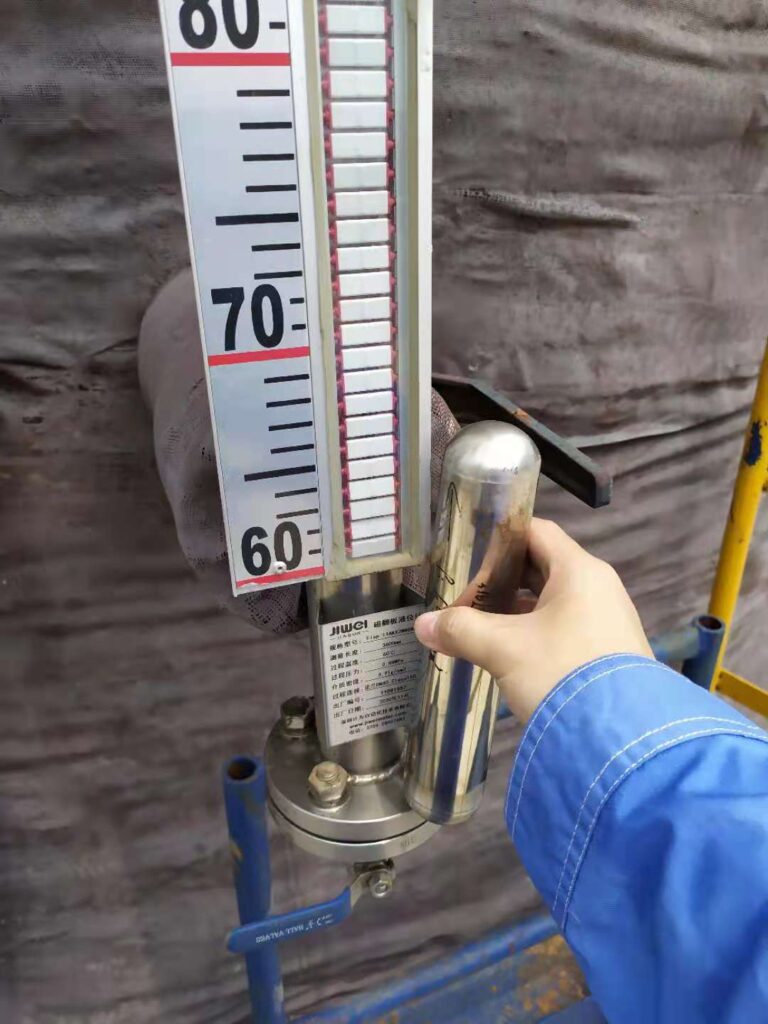
Comparison of Maintenance and Service Life
Key maintenance challenges for glass tube level gauges include:
- Glass tube scaling, which affects reading accuracy and requires periodic cleaning.
- Seal deterioration or glass breakage, necessitating frequent replacements and increasing long-term operational costs.
In contrast, magnetic level gauges require minimal maintenance:
- No glass components, eliminating breakage risks.
- Excellent sealing, ensuring long-term reliability with only periodic inspections of the magnetic float and indicator.
- No mechanical moving parts, allowing for a service life of over 10 years, significantly reducing maintenance costs compared to glass tube level gauges.
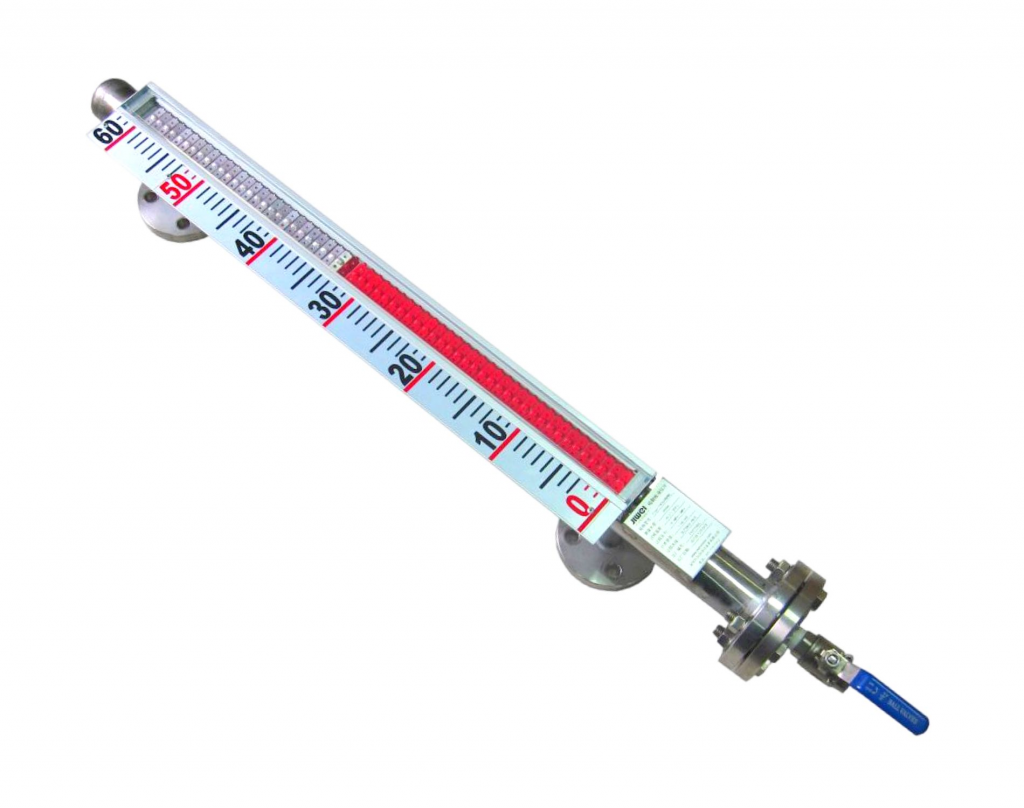
Conclusion: Why Magnetic Level Gauges Are Superior
According to GB/T 21446-2008, magnetic level gauges dominate modern industrial measurement due to their higher safety, adaptability to harsh conditions, remote monitoring capabilities, and lower maintenance costs. While glass tube are suitable for standard conditions, they fail to meet the demands of high-temperature, high-pressure, corrosive, or automated monitoring applications.
Additionally, API 2350, which focuses on safety management in liquid level measurement, does not mandate the use of magnetic level gauges but recommends devices that meet safety requirements (e.g., radar, ultrasonic, and float-based level meters). However, magnetic level gauges are widely adopted in tank level measurement due to their superior safety and automation features.
Overall, for critical level measurement applications in petrochemical, chemical, metallurgical, and pharmaceutical industries, magnetic level gauges are unquestionably the more reliable, safer, and intelligent choice.