Ultrasonic Level Meter Accuracy Issues: Causes & Solutions for Precise Measurement
Introduction
Ultrasonic level meters are popular in industries for their non-contact, precise, and reliable measurement of liquid and solid levels. However, many users face accuracy issues in real-world applications, leading to measurement errors, production inefficiencies, and equipment failures. This article highlights the common causes of these ultrasonic level meter problems, including blind spots, interference, installation errors, and environmental impacts. It also provides expert solutions for troubleshooting and improving measurement accuracy.
1. Common Causes of Ultrasonic Level Meter Inaccuracies
Ultrasonic level meters measure distance by emitting sound waves and analyzing the return signal. While this method is effective, several factors can compromise the accuracy of measurements:
1.1 Temperature Fluctuations and Measurement Drift
Temperature can significantly affect the speed of sound, leading to measurement drift. In environments with large temperature differences, ultrasonic sensors may struggle to maintain accuracy.
Solution:
- Choose ultrasonic meters with temperature compensation to account for temperature-induced changes.
- Regularly calibrate devices to minimize drift caused by temperature changes.
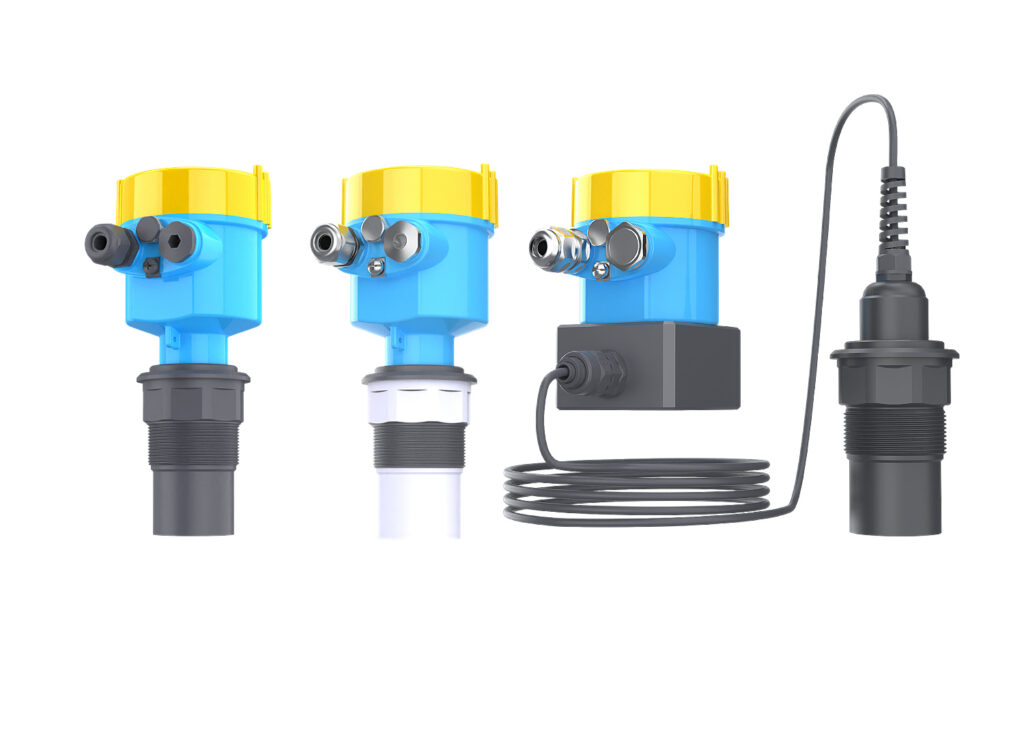
1.2 Steam, Bubbles, and Foam Interference
Ultrasonic signals are highly susceptible to interference from steam, bubbles, and foam on liquid surfaces. These factors scatter or absorb sound waves, causing inaccurate readings.
Solution:
- Install reflectors or shields to reduce interference from steam and bubbles.
- For high-steam environments, consider using radar level meters, which are not affected by steam.
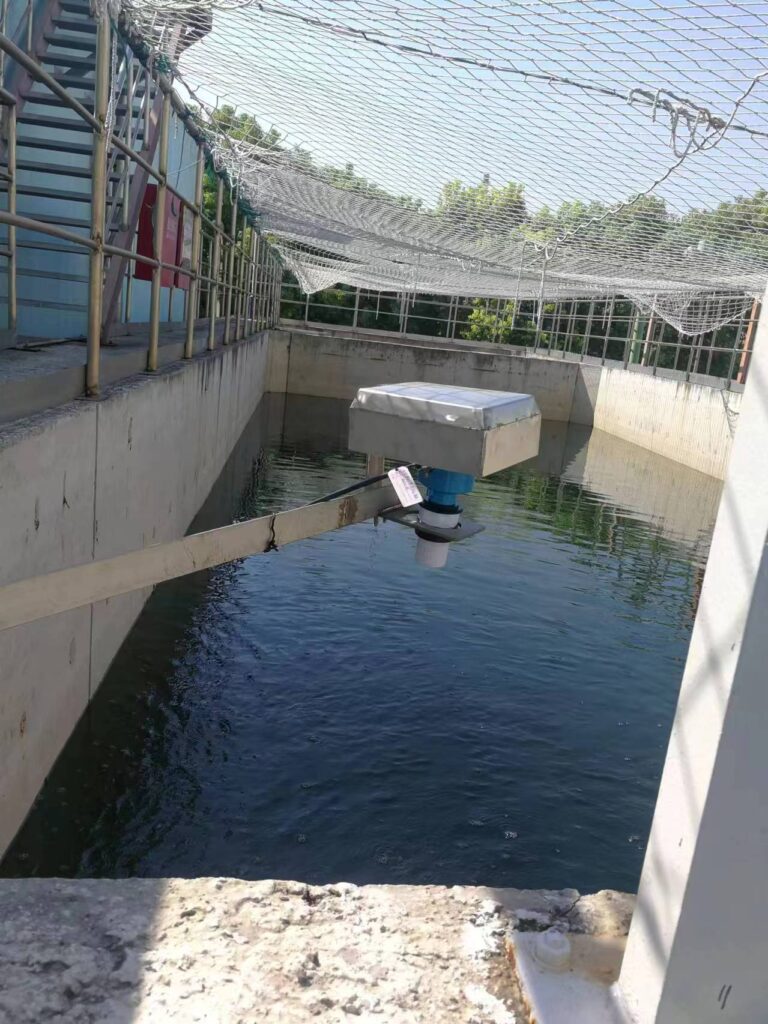
1.3 Blind Spot Problems
Ultrasonic level meters have a minimum range, known as the blind spot, below which they cannot measure the liquid level accurately. If the liquid level falls below this threshold, the meter will fail to register it.
Solution:
- Select level meters with a minimum range that suits your application needs.
- Install the ultrasonic meter at the correct height to avoid reading below the blind spot.
1.4 Incorrect Installation
Proper installation is crucial for accurate ultrasonic measurements. Incorrect mounting angles, improper placement, or environmental obstructions can distort the signal, leading to measurement errors.
Solution:
- Follow installation guidelines carefully, ensuring that the sensor is mounted vertically.
- Avoid installing sensors near high airflow or heat sources that may interfere with signal transmission.
1.5 Environmental Noise and Electromagnetic Interference
Ultrasonic level meters can be affected by external electromagnetic interference (EMI) from industrial equipment or machinery. This interference can distort the signal and result in unreliable readings.
Solution:
- Use ultrasonic meters designed with enhanced EMI resistance to minimize interference.
- Position meters away from sources of electromagnetic noise, such as high-voltage equipment.
1.6 Atmospheric Pressure Fluctuations
Changes in atmospheric pressure, especially in outdoor installations, can affect the speed of sound waves. Variations in pressure can lead to slight measurement inaccuracies.
Solution:
- For outdoor installations, choose ultrasonic level meters that account for atmospheric pressure changes.
- In fluctuating conditions, combine ultrasonic measurement with other technologies like radar for more accurate results.
2. How to Improve Ultrasonic Level Meter Accuracy
2.1 Regular Calibration and Maintenance
Calibrate and maintain your ultrasonic level meter regularly to ensure optimal performance. Clean the sensor periodically to remove dirt and debris that may obstruct the signal.
2.2 Choosing the Right Model for Your Application
Select the appropriate ultrasonic level meter based on environmental conditions. For high-pressure, high-temperature, or corrosive environments, consider more robust models with specialized features.
2.3 Optimized Installation Practices
Proper installation plays a significant role in achieving precise measurements. Install your level meter in a clear line of sight with the surface to ensure unobstructed signal transmission. Avoid areas with excessive turbulence or steam.
2.4 Data Monitoring and Diagnostics
Leverage data analysis tools to monitor the performance of your ultrasonic level meter continuously. If discrepancies arise, investigate potential causes such as environmental changes or equipment malfunction.
3. Conclusion
Ultrasonic level meters are an efficient and cost-effective solution for liquid and solid level measurement. However, to ensure precise and reliable measurements, it’s essential to understand the common causes of measurement inaccuracy. By addressing factors like temperature variations, interference, blind spots, and incorrect installation, you can improve the accuracy and performance of your ultrasonic level meter.
For complex applications or harsh environments, consider integrating radar level meters or other advanced measurement technologies. Regular maintenance, proper calibration, and optimized installation are key to maintaining the performance of your ultrasonic level meters and ensuring consistent, accurate measurements in your processes.
Call to Action (CTA):
If you’re facing accuracy issues with your ultrasonic level meter, contact us for expert troubleshooting and consultation to optimize your measurement system for improved performance and reliability.