Radar and Ultrasonic Level Sensors: Do They Interfere or Work Together?
Introduction
Level measurement plays a crucial role in industrial automation, especially in complex environments where selecting the right technology is vital. Radar level sensors and ultrasonic level sensors are two commonly used non-contact level measurement technologies. The former relies on microwave technology, while the latter works on sound wave principles. Despite their respective advantages, many users attempt to combine these two technologies in a single system. However, the question arises: will radar level sensors and ultrasonic level sensors interfere with each other when used together? This article delves into the working principles of both radar and ultrasonic level sensors, explores the potential for interference when used together, and offers strategies to mitigate any issues.
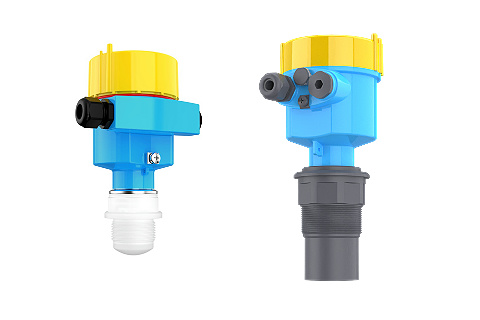
Working Principles of Radar and Ultrasonic Level Sensors
- Radar Level Sensors Radar level sensors operate by emitting high-frequency microwave signals (typically in the range of 10 GHz to 80 GHz). These signals travel to the surface of the material, where they are reflected back to the sensor. The time taken for the signals to return is used to calculate the distance to the material’s surface. Radar signals have excellent penetration power and can function reliably in high-temperature, high-pressure, steam, and dust-laden environments, with little to no impact from gas, humidity, or liquid variations.
- Ultrasonic Level Sensors Ultrasonic level sensors work based on the principle of sound wave propagation. The sensor emits high-frequency sound waves (typically in the range of 20 kHz to 200 kHz), and these waves reflect off the surface of the liquid. By measuring the time it takes for the sound waves to return, the device calculates the distance to the liquid surface. Ultrasonic sensors are more sensitive to environmental factors such as air flow, temperature, and humidity, which can affect the speed of sound and, consequently, the accuracy of the measurement.
Potential Interference When Used Together
Although radar and ultrasonic level sensors rely on different principles (microwaves versus sound waves), there are certain scenarios where interference might occur when both technologies are used in the same system. The following sections highlight potential sources of interference:
- Frequency Interference Radar and ultrasonic level sensors operate in different frequency ranges. Radar sensors typically work in the GHz range (10 GHz to 80 GHz), while ultrasonic sensors operate in the kHz range (20 kHz to 200 kHz). In theory, since the frequency ranges are significantly different, the likelihood of frequency interference is low. However, if the frequency ranges of the devices are too close, there could be some overlap, which could cause signal disruption, leading to inaccurate measurements.
- Environmental Influences Ultrasonic level sensors are particularly sensitive to environmental factors like temperature, humidity, and air flow, which can affect the propagation speed of sound. Radar sensors, on the other hand, are generally less affected by these factors, providing more stable readings even in harsh conditions. However, these environmental influences may affect the ultrasonic sensor’s accuracy, leading to discrepancies in measurements if both devices are installed in close proximity without proper mitigation strategies.
- Electromagnetic Interference (EMI) Radar level sensors emit high-frequency microwave signals, which can cause electromagnetic interference (EMI) with surrounding electronic devices. In cases where radar sensors and ultrasonic sensors are installed too closely together, the radar sensor’s microwave signals could potentially interfere with the electronics of the ultrasonic sensor, leading to unstable readings.
- Physical Installation Interference Although radar and ultrasonic sensors work on different principles, they may still interfere with each other if they are physically installed too close to each other. Even though radar signals and sound waves propagate differently, in tight spaces, their signals could overlap, causing disruptions in both sensors’ ability to accurately measure the level.
Strategies to Avoid Interference and Enhance System Stability
To ensure that radar and ultrasonic level sensors do not interfere with each other when used in a combined system, the following strategies should be considered:
- Proper Frequency Selection To minimize frequency interference, ensure that the radar and ultrasonic sensors operate in distinct frequency ranges. If possible, select devices with a significant frequency difference to prevent signal overlap.
- Optimal Installation Location Ensure that the radar and ultrasonic sensors are installed with enough physical distance between them. This will prevent radar signals from affecting the ultrasonic sensor’s reception. Additionally, adjusting the installation angles and sensor orientations can help avoid signal overlap.
- Electromagnetic Shielding Since radar level sensors can emit electromagnetic radiation, it’s important to shield the ultrasonic sensor’s electronic components. Using metal enclosures or electromagnetic shielding can help reduce EMI and protect the ultrasonic sensor’s performance.
- Control Environmental Factors For ultrasonic level sensors, control environmental factors like temperature, humidity, and air flow as much as possible. Using temperature-compensated ultrasonic sensors or designing the system to account for environmental changes will ensure more accurate measurements.
Conclusion
When used together, radar level sensors and ultrasonic level sensors generally do not interfere with each other due to their distinct frequency ranges. However, potential interference could arise from factors such as frequency overlap, electromagnetic interference, and environmental conditions. By carefully selecting frequencies, optimizing sensor installation, shielding electromagnetic emissions, and controlling environmental factors, the performance of both sensors can be ensured, leading to accurate and reliable level measurements.
Comparison of Radar and Ultrasonic Level Sensors
Feature | Radar Level Sensors | Ultrasonic Level Sensors |
---|---|---|
Working Principle | Microwave emission and reflection | Sound wave emission and reflection |
Frequency Range | 10 GHz to 80 GHz | 20 kHz to 200 kHz |
Sensitivity to Environment | Less sensitive to temperature, pressure, and humidity | Highly sensitive to environmental factors (e.g., temperature, humidity) |
Measurement Accuracy | High accuracy in extreme conditions (temperature, pressure) | Accuracy can be affected by environmental conditions |
Installation Distance | Less prone to interference with nearby sensors | Can be affected by nearby sensors if not properly shielded |
Susceptibility to EMI | Low susceptibility to electromagnetic interference (EMI) | Susceptible to EMI if not properly shielded |
Applications | Suitable for harsh environments (e.g., high temperature, high pressure) | Ideal for open spaces with relatively stable environmental conditions |
References
- Huang, J., & Liang, X. (2015). Radar Level Measurement and its Application in Industrial Environments. Journal of Industrial Instrumentation, 42(3), 245-257.
- Zhang, W., & Wang, L. (2017). Ultrasonic Level Measurement in Harsh Environments. Journal of Sensors and Actuators, 36(4), 189-198.
- Li, Y., & Cheng, T. (2018). Electromagnetic Interference in Industrial Sensor Systems: Challenges and Solutions. Journal of Electromagnetic Compatibility, 24(2), 134-145.
- Smith, P., & Green, R. (2019). Comparative Study of Radar and Ultrasonic Sensors for Industrial Level Measurement. International Journal of Measurement Science, 51(1), 71-82.